Salt Vault Replaced with Automated Salt Brine System
Johnsonville Sausage, Momence, ILSituation
A large meatpacking plant was utilizing a salt-vault installed in the interior of the mechanical building. The salt was blown in by a pneumatic truck through piping. Over the years, significant leaks in the salt-fill mechanism developed allowing salt dust to blow out into the mechanical room, causing corrosion damage to the equipment in the area. Additionally, the salt vault filled with sediment resulting in very low saturation of the brine, requiring frequent regenerations of the water softener.
In an effort to supplement the system they were using bag salt and manually loading salt into the day-tank of the softener to increase the saturation, but this was unsuccessful and very labor-intensive.
Challenge
- Supplying consistent >95% saturated brine (old salt vault would only produce ~30% saturation)
- Prevention of salt dust entering the mechanical room
- Eliminate the need to store and handle bag salt
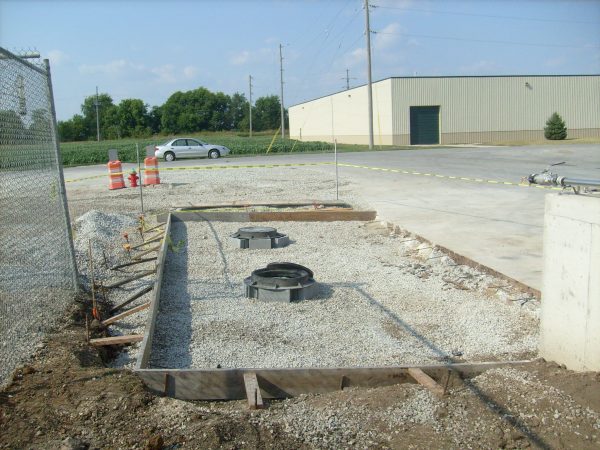
Solution
To meet the needs of the facility an 8000-gallon bulk AUTOBrine® System was installed. The AUTOBrine® System was located outside the facility. The system, with an on-demand
sequencing system now supplies >95% saturated brine to the water softeners.
Unlike the salt vault that was not accessible to clean, the AUTOBrine® System is cleaned at a predetermined salt use interval to maintain high-quality clean brine for water conditioning. Salt dust no is longer an issue in the mechanical room; therefore, equipment replacement costs have been reduced. This also eliminated the manual handling of bag salt.
Results
- $28,800 Operations Cost Savings Annually
- > 60,000 lbs. of carbon footprint reduction to date
- Eliminated Workers’ Compensation injury from salt handling
- Salt storage space elimination
- Eliminated salt dust in mechanical room reducing the need for equipment replacement
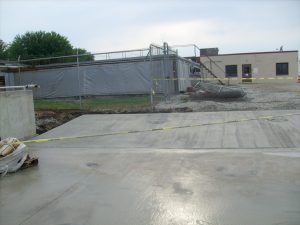